Anybus-IC - Technical Specifications |
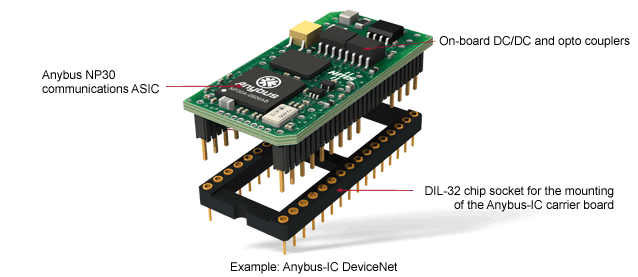
Functionality of the Anybus-IC
Anybus-IC is a family of single chip communication solutions. The interfaces contain the complete functionality of an industrial network interface and provide a standardized and network independent application interface for the host automation device.
Whether fieldbus, or industrial Ethernet is needed, these small, flexible and inexpensive interfaces are the perfect fit for the communication requirements of small and medium automation devices. Anybus-IC provides a compelling alternative to extensive in-house development.
For intelligent automation devices with their own microprocessor, the Anybus-IC is 连接ed via its serial UART interface and thus provides advanced communication functionality including cyclic I/O data, acyclic parameter data and network status/diagnostic information.
For automation devices without a microprocessor, the Anybus-IC provides direct input and output signals via a clocked shift register interface.
The Anybus-IC is the size of a standard DIL-32 chip socket. It requires only one 5V power supply, and consumes very little power. It also provides a full galvanic isolated network interface.
Supported network features
Anybus-IC incorporates the latest protocol specification of the chosen network. HMS continuously maintains the network functionality of the Anybus-IC so that your automation device always complies with the latest standards and has unlimited interoperability. All Anybus-IC modules are pre-certified for full network compliance with the chosen network. The network functionality includes cyclic I/O data, acyclic parameters, network, status and diagnostic information, alarm messaging and device identification. Through the host application interface the Anybus-IC functionality can be adapted to the communication requirements of the automation device.
IT Functions for Ethernet versions
The Anybus-IC Ethernet versions contain embedded IT functions such as, an embedded dynamic web server, Telnet server, FTP server and an Email client.
For example, together these IT functions allow data to be monitored via the built in web server, or using event triggered Email messages. SSI technology enables web pages and Email messages to carry dynamic content such as I/O data, configuration, and settings and then visualizing in a user friendly way.
The IT functions also include a TCP/UDP/IP socket interface. This allows applications to execute any kind of vendor specific TCP/IP based protocols using the core functionality of the Anybus-IC.
KEY TECHNICAL FEATURES |
Family of complete fieldbus/Ethernet interfaces with the size of a DIL-32 chip socket |
Works as a stand-alone fieldbus/Ethernet interface or together with an其他 micro controller |
Contains all analog and digital components for full network 连接ivity |
Complete and network protocol on-board |
Fully galvanic isolated network interface |
SCI serial host interface with 128 bytes Input and 128 bytes Output data via Modbus-RTU |
SSC shift register interface with 16 bytes direct Input and 16 bytes direct Output data |
Ethernet versions include extended IT functions |
Single 5V power supply with very low power consumption |
Pre-certified for fieldbus/Ethernet conformance - CE, UL, RoHS compliance |
Anybus-IC application examples
Anybus-IC has been optimized for field devices, where small size and multiple network 连接ivity are important. Anybus-IC contains all electronic components and software necessary to implement a full featured industrial communication interface. Applications such as valve manifolds, and intelligent sensors / actuators are just some of today’s products that are successfully using Anybus-IC.
Case examples:
Valve manifolds
Within a valve manifold, the Anybus-IC can be used to directly interface the electric, magnetic or hydraulic valve drivers. This is made via the SSC shift register interface of the Anybus-IC. The output data received from the fieldbus/Ethernet interface is used to directly open or close the valves. Input data is used to report the position of the valves back to the master on the fieldbus network (PLC). The valve manifold does not necessarily need an own microprocessor as the Anybus-IC provides direct discrete I/O.
Typically, valve blocks are IP65 rated, so the network interface is realized with M12 连接器. The Anybus-IC supports up to 16 bytes of direct discrete input and 16 byte of direct discrete output data via the SSC interface.
Actuators
Intelligent actuators typically have their own microprocessor. In these devices, Anybus-IC is 连接ed via its asynchronous serial SCI interface with the main microcontroller of the actuator. Anybus-IC handles all communication and offloads the microprocessor of the actuator completely from all time critical communication tasks.
Through the fieldbus/Ethernet network interface and the SCI interface of the Anybus-IC, the actuator is parameterized during start-up. During regular operation, the set point for the actuator is transferred as output data via the fieldbus/Ethernet and the Anybus-IC. While the actual position of the actuator is transmitted as input data via the Anybus-IC and the fieldbus/Ethernet network to the master on the fieldbus/Ethernet network (PLC). Via the SCI interface, the Anybus-IC supports up to 128 bytes input and 128 bytes output data.
Hardware Application Interface
A flexible application interface enables the Anybus-IC to operate either stand-alone or controlled by the host microcontroller. A range of communication channels allows fieldbus/Ethernet data ex改变 as well as internal discrete I/O. In addition, data can be mapped between the various channels in a flexible manner without any intervention by the host system.
The Anybus-IC is very small and fits into a standard DIL-32 chip socket to 连接 to the host automation device. It requires a single 5V power supply, and consumes very little power. It also provides a full galvanic isolated network interface.
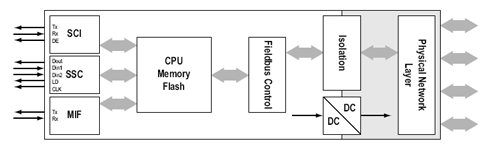
Block schematic - Anybus-IC
Flexible data ex改变 interfaces
Apart from the fieldbus interface, the Anybus-IC features two additional data ex改变 interfaces (SCI and SSC). These interfaces operate completely independent of each 其他 and can be used simultaneously.
Serial Communication Interface (SCI)
Intelligent devices normally have their own micro controller. The serial 2-wire TTL interface (SCI) is used to 连接 the Anybus-IC to the micro controller of an intelligent automation device.
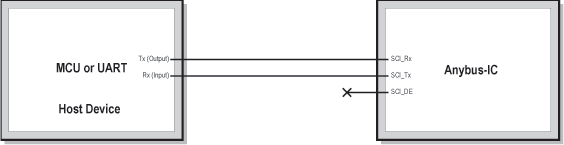
This provides access to internal parameters of the module as well as I/O data ex改变 through the built in Modbus RTU protocol. The communication between the Anybus-IC and the micro controller of the automation device is based on the proven Modbus-RTU protocol. Via the SCI interface, the Anybus-IC supports up to 128 bytes input and 128 bytes output data.
Synchronous Serial Channel (SSC)
The SSC channel is intended to be used with an external shift register loop to form discrete inputs and outputs. It supports up to 17 registers (136 bits) in each direction, out of which 16 (128 bits) can be used for data ex改变.
As illustrated below, the first input and output registers in the shift register loop are by default reserved for fieldbus specific functions. It is possible to disable this functionality and use those registers for data ex改变 instead. The maximum total amount of data is however still limited to 16 registers (128 bits) in each direction. The functionality of the SSC interface also provides an interface for status, diagnostic and status LED indicators and network address switches.

Monitor (MIF) interface
The serial TTL-level MIF-interface provides an easy way to monitor data and access parameters of the Anybus-IC through a terminal based user interface. The use of this interface is optional
Network interface
The signaling of the network interface is network dependant. For all fieldbus versions, just the fieldbus 连接or needs to be added. For Ethernet versions the physical 隔离transformer (PHY) and the Ethernet 连接or must be added. Alternatively, fast- jack Ethernet 连接器 can be used.
TECHNICAL SPECIFICATIONS |
Size:
|
42 x 21 x 15mm (L x W x H) 2.13 x 0.83 x 0.59” (L x W x H ) |
Power Supply:
|
+5 Volt, |
温度:
|
操作-40°C to + 85°C, non-op -40°C to + 85°C |
Env Conformance:
|
RoHS conformance |
EMC Certification:
|
CE marked, UL & cUL conformance |
Conformance:
|
Tested and verified for fieldbus conformance |
SCI Software Interface
The Anybus-IC SCI (serial communication interface) is designed to be network protocol independent, making it possible to support several networks using the same application software. The communication between the Anybus-IC and the host microcontroller is using the proven Modbus-RTU protocol.
The host microcontroller functions as the Modbus-RTU master, while the Anybus-IC functions as the slave. The serial transmission is secured by a CRC checksum which can allow for extended distances between the host microcontroller and the Anybus-IC inside the automation device. The Anybus-IC offloads the host microcontroller from all time critical communication tasks of the selected network. The communication between the Anyus-IC and the host microcontroller is fully under the control of the host microcontroller which mainly defines the level of performance. The transmission speed between the host microcontroller and the Anybus-IC can be selected in a range between 4.8 kBit/s to 57.7 kBit/s with auto baud rate detection by the Anybus-IC.
The Modbus commands are used to read/write cyclic I/O data, acyclic parameters and status, control and diagnostic information. Through the Modbus commands data width and data mapping on the fieldbus/Ethernet network is also initialized.
To speed up the integration of Anybus-IC into the host device, HMS provides free of charge, sample code (C source), to show how the communication between the Anybus-IC and the host microcontroller can be implemented. HMS also supplies a full featured evaluation board with many hardware and software integration tools included.
Data Mapping
Anybus-IC features a flexible memory mapping system. Data received on any of the data ex改变 interfaces can be mapped (i.e 连接ed) to an其他 data ex改变 interface, thus forwarding this data from one interface to the 其他.
This way, the module can be used not only for fieldbus 连接ivity, but also to provide internal I/O inside the application. (i.e by mapping SSC I/O to the SCI serial interface and vice versa)
By mapping fieldbus I/O to the SSC interface, the digital inputs / outputs provided by this interface are instantly available from the fieldbus.
MIF Configuration Interface
The MIF-interface provides an easy way to configure and monitor the Anybus-IC based on an inbuilt configuration interfaces, accessed by a standard PC terminal emulation program, such as Windows™ Hyper Terminal. The use of this interface is optional, but it provides access to the various parameters of the Anybus-IC, as well as functions for data monitoring and configuration.