Flexible and cost-effective solution for the integration of Industrial Ethernet
Highlights
The Industrial Ethernet Module provides customers with a universal interface for the integration of various Industrial Ethernet technologies into their products. The area of application is wherever intelligent devices such as drives, frequency converters, IO-modules, valves and 其他 components of automation technology are to be equipped with Industrial Ethernet and for which flexibility and extendibility in conjunction with transparent costs are important.
The following technologies are supported:
- EtherCAT (Slave Controller)
- EtherNet/IP (Adapter Device)
- Powerlink (Controlled Node)
- PROFINET RT (IO-Device)
- sercos (Slave Device)
Other Industrial Ethernet technologies are available soon:
- Modbus/TCP (Server Device)
描述
of functions of the Industrial Ethernet Module
The Industrial Ethernet Module is based on an Altera Cyclone III FPGA. An integrated CPU is responsible for processing the Industrial Ethernet protocol and data ex改变 via the host interface. It also has 8 MB RAM to run the protocol software and 2 MB FLASH from which the software and the FPGA design are loaded.
Support of the various Industrial Ethernet protocols is implemented universally and flexibly. In the FPGA, an Industrial Ethernet Controller which is ideal for the relevant technology is used for this.
Industrial Ethernet Module - Block Diagram
The two Ethernet interfaces are fed out independently of each 其他, so that different topologies can be implemented in accordance with the various Industrial Ethernet standards:
- Line topology for EtherCAT, Powerlink and sercos
- Star topology for EtherNet/IP, Modbus/TCP and PROFINET
Due to the flexibility which the FPGA technology offers the customer and the universal implementation of the Ethernet interface, the Industrial Ethernet Module can be easily extended to future standards such as line topology for EtherNet/IP and PROFINET.
Using the open programming interface on the host CPU, the Ethernet Module Interface (EMI), customers can easily integrate the Industrial Ethernet Module into their existing systems. The counterpart on the module is the Bus Protocol Wrapper (BPW), which abstracts the functions of the Industrial Ethernet protocol to such an extent that users can implement their applications via the EMI independently of the underlying network. In addition, they can also use protocol-specific features on the application side.
Programming Interface of the Industrial Ethernet Module - Block Diagram
The host interface is implemented as a general µC interface. Alternatively, a Serial Peripheral Interface (SPI) is available. The Industrial Ethernet Module and the host CPU have up to 16 KByte shared data memory. The data memory is physically implemented in the FPGA as a real Dual-ported RAM in order to ensure the efficiency of the interface even for high-performance applications such as servo drives or fast IOs.
With the also available evaluation kit, the Industrial Ethernet Module can be directly 连接ed to the processor module of Phytec (phyCORE-XC161). This solution is therefore ideal for rapid prototyping.
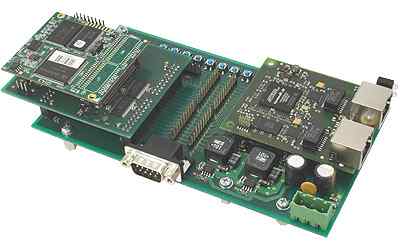
On request, the Industrial Ethernet Module can be fully implemented as a design-in in the customer’s device. This enables customized adaptations or the integration of further components or interfaces in the FPGA.
The technical details and functions of the Industrial Ethernet Module may 改变.