The powerful tool for analysis of the CAN bus physics and the CAN protocol

Typical faults during the operation of CAN bus systems, such as node failure, communication errors or complete system failure, are often caused by problems in the bus physics. Generally, devices which transmit messages with a low signal-to-noise ratio are highly susceptible to failures. The CAN-Bus-Tester provides an overview of the signal-to-noise ratios on the bus, enabling frequent causes of failures to be quickly identified and rectified. In addition, the most important logical analysis functions are also integrated into the Tester (otherwise found only in protocol analyzers).
The tester can be used for CAN bus systems with 11- or 29-bit identifier in accordance with ISO 11898-2 and supports as basis version the CAN layer-2 protocol. Using add-ons, the CBT can also support CANopen, DeviceNet and SAE J1939 based systems. This support can be enabled on the device at any time using the corresponding licenses. Automatic baud rate detection and the self-connecting BusScan allow the CAN-Bus-Tester to be quickly and easily connected to the system to be analyzed and started. The measurement results are automatically assigned to the relevant CAN identifiers or network nodes.
IXXAT also offers a CAN Monitor Tool (Receive/Transmit) as an add-on for the CBT, providing a new and freely scalable user interface which allows to use the advantages of high resolution displays. The tool displays the CAN messages, error frames and overrun frames. It allows to trigger on telegrams and comes with a function to display start/stop and pause notes in the reception window. Furthermore, in transmission mode the CAN telegrams can be collected within a list (sequences), which allows to send several CAN messages with defined time intervals, once or repeatedly.
Depending on the test strategy, various methods of identifying faults can be used, such as a fast overview of the complete system, monitoring of an individual node or setting various trigger events (physical and/or logical faults and error-frames). When the trigger function is used, all faults are defined up to the individual bit position, are provided with a time stamp and displayed in the integrated oscilloscope.
A trigger signal available via the external trigger output can be used to trigger an oscilloscope. A certain CAN message or an error telegram can thus be displayed selectively on the oscilloscope.
With the CAN-Bus-Tester 2, the bus wiring can be tested while the system is being set up and its transmission properties can be saved. During the complete lifetime, comparative measurements can be carried out directly on the running system and thus downtimes prevented.
The CAN-Bus-Tester is connected to a Windows PC via USB and operated with the software supplied. The measured values determined can also be saved or summarized in a detailed report. Logging data from the CANobserver can also be imported for inspection.
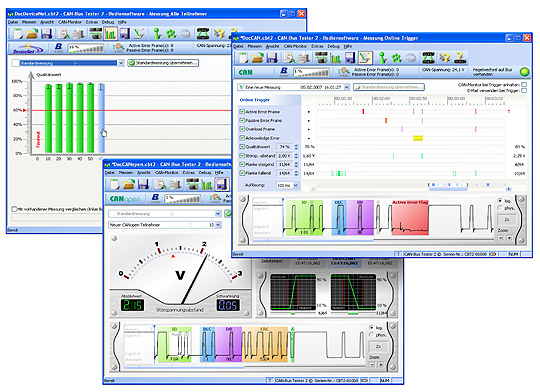
Highlights
- Analysis of the signal-to-noise ratio of all telegrams (level, flanks, faults)
- Integrated oscilloscope with data interpretation for telegram analysis
- Comprehensive trigger conditions for fault localization (logical and physical errors)
- Monitoring of bus status, bus load, error telegrams
- Wiring test (termination resistance, short circuits, interruptions, loop resistance, line length)
- Integrated CAN monitor for transmission and reception of CAN messages
- Automatic baud rate detection
- Simple connection to CAN systems thanks to automatic baud rate detection and BusScan
- Simple operation via Windows program
- Simple generation of test protocols