The specification and implementation of communications protocols has been a main focus of IXXAT's activities for more than 20 years. Besides the specification of customer specific protocols, we do offer the development of protocol software, the implementation on devices and the development of test environments and methods.
Our range of services for communication protocols includes
- Specification of communication protocols
- Development of protocol software
- Implementation of protocol software in devices and components
- Development of test environments and testing methods for protocol implementations
- Development of safety-related protocol software in accordance with IEC61508
Example projects:
CAN-based protocol suite for data
communication in elevators
Development of a comprehensive, scalable protocol suite for data communication in elevators. Design, implementation and testing of transport protocols of various performance levels. Network management and system services based on the extended CAN format. Porting of the protocol suite to several controller platforms and development environments. 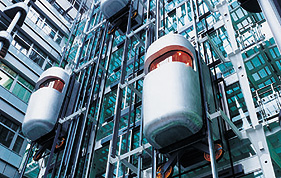
CANopen-based protocol suite for data
communication in marine automation applications
Development of the complete protocol software for data communication in marine automation, integration of the communication software in the various automation components of the manufacturer. Support of the manufacturer in overall system start-up. In this comprehensive development project, practically all complex mechanisms specified for CANopen were used, or certain extensions (e.g. Flying Master principle, redundant data communication in accordance with the hot-standby principle) were also to be implemented. From completion of the development work onwards, IXXAT is responsible for the management and further development of the complete communication software.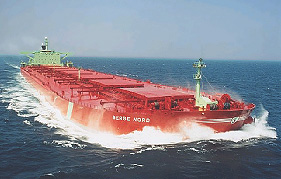
Implementation of CANopen in small SPS
A CANopen connection was implemented for a small SPS. The CANopen interface was connected to the SPS via an SPI interface and the data exchanged between the SPS and the CANopen interface via a specific protocol. The main requirements here were the limited memory on the CANopen interface and loading of the configuration data from the SPS. In addition to the specification of the interface, IXXAT carried out the implementation and testing of the CANopen interface.Implementation of CANopen/DeviceNet
in standard I/O module
A modular I/O system was extended with an interface for CANopen and DeviceNet. The main requirements of the customer were a uniform hardware platform for both protocols and the availability of both fieldbuses on one module. Based on a specification developed together with the customer, IXXAT carried out the software development and the integration of the CANopen and DeviceNet protocols in the customer's product.Implementation of DeviceNet in sensor module (Inficon)
An interface for DeviceNet was developed for a vacuum sensor as used in the production of semi-conductors. The device supports the profile for vacuum/pressure gauges defined by the ODVA (Open DeviceNet Vendor Organisation) in cooperation with SEMI (Semiconductor Equipment and Materials International). IXXAT carried out the complete software development and integration of the DeviceNet protocol in the customer's device.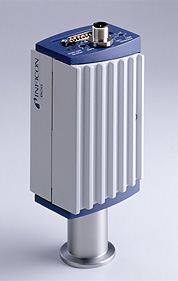
Implementation of Ethernet/IP in valve island (Festo)
A modular valve island, consisting of different electrical and pneumatic components, was extended with an interface module for EtherNet/IP. The functionality of the interface module was specified together with the customer. IXXAT also carried out software development and integration of the EtherNet/IP protocol in the customer-specific hardware.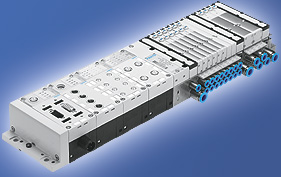
Integration of Ethernet Powerlink in a drive
The IXXAT EPL Stack for a controlled node was implemented on an interface board based on the Freescale MCF 5275 and connected to the DSP drive host. A serial connection and a host port interface were used for the communication interface between the host and the interface board. Via the serial interface the EPL interface board receives commands with a specific protocol from the DSP. These commands are processed in the EPL application.The host port interface is used for the exchange of process data with the host system and for acyclic reading and writing of object data of the host system via SDO. Object accesses (CANopen object addressing in DSP addressing format conversion) are also implemented on the EPL interface board.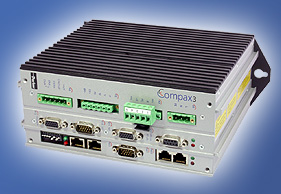
Protocol layer for safety-related communication
IXXAT developed a concept for EPLsafety protocol software in accordance with the EPLsafety profile specification of the EPSG (ETHERNET Powerlink Standardization Group) with the functions SSDO, SPDO, SNMT, SCM, SOD and the necessary EPLS API functions in accordance with SIL3 of EN61508. The software must be called cyclically. The cycle time essentially determines the data throughput, as only one message per call at most is compiled for transmission or one received message unpacked and analyzed.The software supports several EPLS domains, so that an EPLS gateway can also be implemented.Apart from requesting and releasing memory blocks for EPLS frames, the EPLS software does not require any further functionality of the platform. The software is tested by IXXAT on a reference target system, released and certified. Two demo applications (SCM and SN) are supplied together with the EPLS software that facilitate initial use of the software.The scope of supply also includes a user's manual in English in accordance with the safety directives.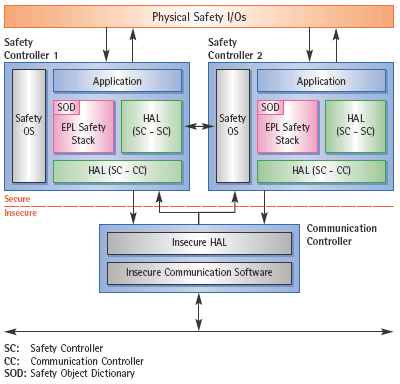