PROFINET is the innovative, open standard for real-time industrial Ethernet in automation technology. The PROFINET Standard is specified and published by PI (Profibus & PROFINET International – http://www.profibus.com).
PROFINET provides solutions for process automation, factory automation and motion control. PROFINET enables the integration of existing fieldbus systems, like Profibus, Interbus, devicenet and 其他 technologies to an open Ethernet based network.
PROFINET uses Ethernet standard as well as TCP, UDP and IP as protocols for communication, configuration and diagnosis in the network.
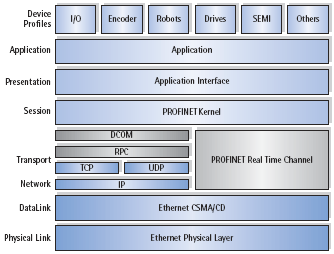
The PROFINET standard defines three different performance levels which cover the various requirements from different applications.
For non-realtime applications, PROFINET NRT (Non Real Time) is defined. It uses standard protocols as UDP/IP. With cycle times > 100 ms PROFINET NRT targets for applications in process automation.
For applications with higher requirements on cycle time like factory automation, PROFINET RT (Real Time) is the right choice. I/O data is ex改变d directly using the Ethernet protocol, while diagnosis and configuration uses standard UDP/IP. PROFINET RT enables applications with cycle times > 10 ms.
The highest requirements come from the control of complex industrial drive systems like packaging machines or robotics. With PROFINET IRT (Isochronous Real Time) applications with cycle time < 1 ms and jitter < 1 µs are possible. This is accomplished by the usage of specific hardware for the Ethernet interface.
On the application side three different device types are defined: IO-Controller – the classic PLC (Master), which establishes 连接ions to the devices, ex改变s data and controls the system, IO-Device – the device (Slave) which is assigned to the controller to ex改变 data, and IO-Supervisor – the interface for programming, commissioning and diagnosis in the network.
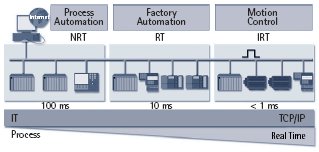
Beside communication and ex改变 of I/O data the PROFINET standard also defines the topology and structure of the network. Guidelines for the cabling, the selection of suitable 连接器 and topology components facilitate the planning and the commissioning of a PROFINET network. The user has the choice between a star structure using (managed) switches which is common in IT business, the classical line structure used in profibus systems and tree structure which combines both principles.
The migration of existing Profibus systems to real-time PROFINET systems can easily be achieved by using Proxies (网关s) which enable the communication and the data ex改变 between both networks.
The device profiles already known from the Profibus world can also be used for PROFINET. With PROFIdrive a powerful profile for the implementation of high-performance drive solutions is available.
For safety-relevant applications, the PROFIsafe profile for PROFINET and Profibus DP systems is defined.